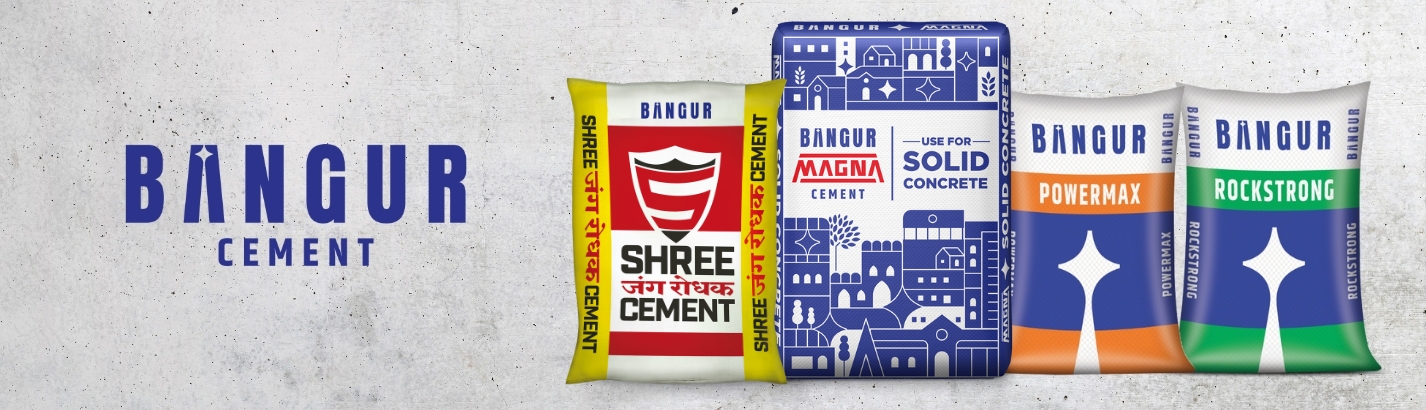
Cement Bag Prices and Other Factors That Influence Construction Costs
- Feb 14
- 4 min read
Estimating the costs of a construction project is an important step. So whether you are building your dream home or a commercial structure, a well-prepared budget is very necessary to make sure that your building project remains on track financially thereby keeping away from facing any sort of unexpected expenses and/or delays.
In this article, we are going to break down some of the major factors that are essential for the work of construction cost estimators and explain how to estimate expenses effectively by providing practical tips to help you manage your budget wisely.
The Key Factors That Affect Construction Costs
It is very necessary to understand the major cost components of any construction project that are:
Raw Materials – Cement, sand, gravel, steel, bricks, and other materials.
Cost of Labour – Wages for labourers and other workers.
Equipment – Costs for renting or purchasing necessary tools.
Permits & Approvals – Legal expenses related to construction permissions.
Miscellaneous Expenses – Transportation, storage, and waste management costs.
Each of these factors contribute to the final construction budget, making accurate estimation a very important thing.
Cement Bag Price and Its Role in Budgeting
Concrete happens to be one of the most important materials for any construction and cement being its primary binding component, it is very important to estimate the costs of cement when you are making a budget for construction. Usually cement bag price depends on various factors, such as brand and grade, discounts for purchasing in large quantities, and regional fluctuations in price variations as per transportation and local demand. To estimate cement costs, you should first determine the volume of concrete required for your project. Typically, one bag of cement (50 kg) can produce around 0.0347 cubic meters of concrete when mixed with sand and aggregates. If you want to receive proper estimates, you can get a quote from us that might be suitable and affordable as per your construction needs.
Follow these Steps when Estimating Construction Costs:
Define Your Project Scope
Before estimating costs, have a clear understanding of the project's size and complexity.
Use a Construction Cost Estimator
While manual calculations can be done, many construction professionals rely on construction cost estimator tools that consider the factors like the total area to be built, the type of structure, and the quality of materials selected, thereby giving a detailed estimate.
Calculate the Cost of Ready-Mix Concrete vs. On-Site Mixing
For larger projects, ready-mix concrete is a convenient option. It eliminates the need for on-site mixing and ensures a consistent mix ratio. Comparing these costs can help determine which option is more cost-effective as per your project’s nature.
Factor in Labor and Overhead Expenses
Labor costs vary based on different factors so before hiring professionals, getting multiple quotes from contractors can help determine a fair price. Overhead costs such as material transportation, equipment rental, and site supervision should also be considered in the budget.
Account for Contingencies
Unexpected costs can arise during construction, whether due to material wastage, delays, or design changes. Setting aside 10-15% of the total budget for contingencies ensures that the project runs smoothly.
Construction Tenders and Their Role in Budgeting
Construction tenders can provide competitive pricing from contractors and suppliers when you are working on a large-scale building project. Therefore reviewing multiple bids helps in selecting the most cost-effective option without compromising on quality because these tenders outline everything from scratch starting from material requirements, labor charges, to project timelines, thereby offering a structured approach to budgeting.
5 Practical Budgeting Tips to Save Costs Without Compromising Quality
Compare Cement Prices Before Purchasing – Prices can vary between suppliers, so it’s advisable to check multiple sources.
Order Materials in Bulk – Bulk purchasing often results in lower costs per unit.
Optimize Material Usage – Avoid overordering and reduce wastage by calculating precise quantities.
Consider Alternative Construction Methods – Using prefabricated materials or alternative mixes can sometimes reduce costs.
Hire Skilled Labor – While hiring cheaper labor might seem cost-effective, skilled workers reduce errors and material wastage.
Plan Smart and Build Efficiently
Estimating the costs of construction in an accurate way is key to a smooth and financially sustainable project. So whether you are working on a small home renovation or a large-scale building project, careful planning, smart purchasing and decisions, along with efficient budgeting will definitely make sure that your project stays within financial limits.
At Bangur Cement, we provide high-quality cement at competitive prices, ensuring strength and durability for all your construction needs. Contact us today.