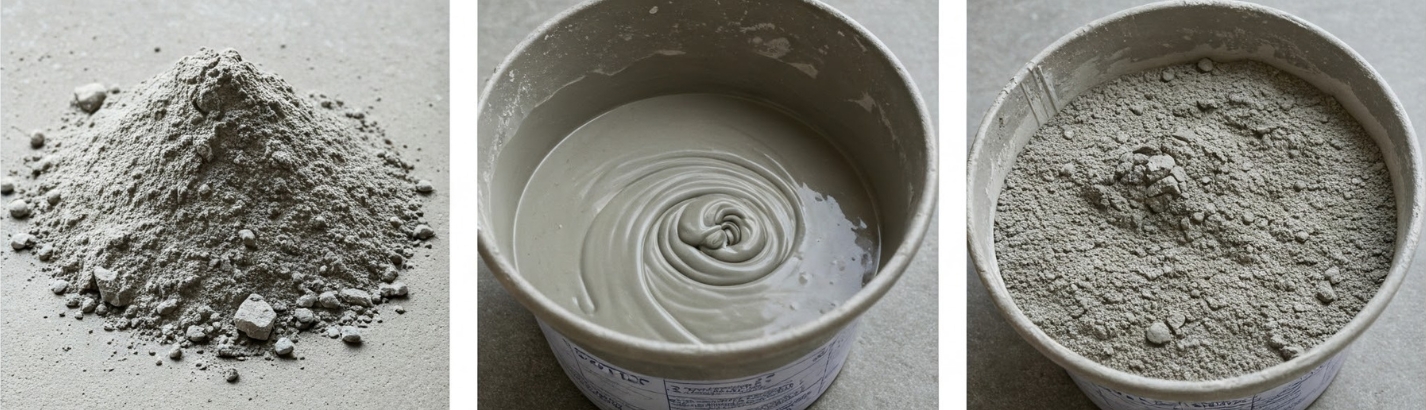
Choosing the Best Cement for Your Construction Project: Insights into OPC, PPC, and Bangur Cement Quality
- Apr 17
- 9 min read
When choosing cement materials for your construction project, you need to select the optimal blend because it affects both project cost efficiency and structural strength and weather resistance. The cement market now offers numerous options, and India is no different than other countries in mainly choosing between Ordinary Portland Cement (OPC) and Portland Pozzolana Cement (PPC). In this article, we have disclosed the full spectrum of information about OPC and PPC cement that will guide readers to buy cement based on their composition, usage, advantages, and cost for their upcoming project.
We shall also delve deeper to study the composition, price, and benefits of PPC and OPC for a detailed comparison of both.
Understanding Cement OPC
OPC stands as the primary cement form that builders utilize in worldwide construction operations. When set, OPC looks like Portland stone, which led to its naming as 'Ordinary Portland Cement.' Gypsum together with clinker undergoes grinding to create this cement, which contains a minimal gypsum addition.
Composition of OPC:
OPC consists primarily of:
Calcium oxide (CaO): 60-67%
Silicon dioxide (SiO₂): 17-25%
Aluminum oxide (Al₂O₃): 3-8%
Iron oxide (Fe₂O₃): 0.5-6%
Gypsum (CaSO₄·2H₂O): 2-3%
This composition is responsible for OPC's distinctive properties of rapid setting and high early strength. OPC is produced by heating limestone and clay to about 1450°C to generate clinker, which is then ground with gypsum to form the final product.
Grades of OPC:
In India, there are three main grades of OPC:
OPC 33 Grade: Has a compressive strength of 33 MPa at 28 days;
OPC 43 Grade: Has a compressive strength of 43 MPa at 28 days;
OPC 53 Grade: Has a compressive strength of 53 MPa at 28 days.
The higher the grade number, the stronger the grade, and usually the higher the price.
OPC cement price in the Indian market:
As of early 2025, cement prices in India vary by region, brand, and grade. However, approximate price ranges per 50kg bag are:
OPC 33 Grade: ₹370-₹410
OPC 43 Grade: ₹390-₹430
OPC 53 Grade: ₹410-₹450
Understanding Portland Pozzolana Cement (PPC)
PPC is a blended cement that is produced by blending OPC along with pozzolanic materials, including fly ash, volcanic ash, or silica fume. This cement has grown in popularity due to the positive environmental aspects and enhancements that it is capable of providing to your new house construction.
Portland cement composition:
OPC clinker: 65-80%
Pozzolanic materials (primarily fly ash): 20-35%
Gypsum: 2-3%
The pozzolanic materials in PPC undergo a secondary reaction with calcium hydroxide formed during the hydration of cement. This further develops cementitious compounds and will contribute to strength gains as time progresses.
Price Comparison in the Indian Market:
PPC: ₹350-₹400
PPC typically is 5-10% less expensive than similar grades of OPC; as such, it is a cost-effective option for many building projects. There may be variations in price based on location, costs to transport it to that location, local taxes, and market conditions.
Comprehensive Comparison: Difference between OPC and PPC
Criteria | OPC | PPC |
---|---|---|
Strength Development | Gains strength quickly in the first 7 days, achieving approximately 70-80% of its 28-day strength. It is best for projects which quickly require the form to be removed or bulk loading to begin early | Gains strength slower at first but will continue to gain strength over a longer period and possibly have a higher ultimate strength after 90 days. The advantage of the extended hydration process is that it produces a denser concrete matrix. |
Durability | Provides adequate durability under normal conditions but is likely to be more susceptible to chemical attack and weathering over time. | Provides improved resistance to sulfate attack, chloride penetration, and alkali-silica reaction due to its finer porous structure. The lower permeability means PPC concrete is less prone to corrosion of the reinforcement. |
Workability | Provides standard workability but may require additional water-reducing admixtures for better flowability. | Offers enhanced workability due to the spherical shape of fly ash particles, requiring less water for the same slump and resulting in improved pumpability and placement. |
Heat of Hydration | Provides adequate workability but may need additional water-reducing admixtures for increased flowability. | Allows for better workability because of the spheres of fly ash particles requiring less water to achieve equal slump, improving pumpability and placement. |
Environmental Impact | Possesses a greater carbon footprint because the process of making clinker takes a lot of energy and releases a significant amount of CO₂. | It is more eco-friendly since it consumes industrial by-products, such as fly ash, to replace the clinker amount and reduce the carbon footprint typically associated with this by as much as 30%. |
Applications | Most appropriate for applications requiring early high strength, for example, precast elements, rapid construction, or low temperatures. | Suitability includes use in infrastructure applications such as highways, bridges, marine structures, and underground structures, where durability is critical. |
How to choose PPC vs. OPC?
You can make a sound decision that weighs performance, durability, cost, and environmental concerns regarding OPC versus PPC cement by considering the following against your project specifications.
Construction Schedule: If quick strength development is a priority, then OPC might be a better option.
Environmental Context: If the structure would be exposed to aggressive environments, PPC's superior durability would be the better choice.
Project Size: If working on a larger project, PPC's decrease in heat generation and cost will be beneficial.
Sustainability Goals: If environmental impact is paramount, then PPC has significant advantages.
Budget: PPC's low cost leads to a decision that is more fiscally responsible on larger jobs.
How good is Bangur Cement for building homes in India?
Choosing a cement brand in India is important because it affects your house’s structural integrity, durability, and lifespan. When you ask the question: “Which cement is best for house construction in India?” you are in need of quality cement that is resistant to the elements and inhibits damage from water, reduces the need for repairs and maintenance, and protects your family's welfare sometimes for generations—likely protecting your single largest investment.
10 factors that make bangur cement quality one of the best in India
Bangur Cement's superior compressive strength, durability, and resistance to chemical attacks make it a standout product in the OPC and PPC markets. It is perfect for a variety of construction demands throughout India because of its advanced manufacture, which guarantees continuous quality.
1. Superior Strength Development
Bangur OPC provides exceptional early strength, crucial for faster construction timelines in residential projects
Bangur PPC offers progressive strength gain, ideal for long-term durability in family homes
Both variants consistently exceed industry strength standards, providing structural integrity for various architectural designs
2. Versatility for Architectural Designs
Particularly well-suited for circular buildings due to superior cohesiveness and workability
Permits thinner sections while maintaining structural integrity, enabling creative curved designs
Supports complex geometrical structures without compromising on strength parameters
3. Enhanced Durability Features
Engineered for superior resistance to environmental deterioration
Bangur Portland Pozzolana Cement provides exceptional protection against sulfate attack in moisture-prone areas
Lower permeability in cured concrete protects embedded reinforcement from corrosion
4. Workability Advantages
Exhibits excellent flowability, critical for achieving smooth finishes in circular buildings
Maintains consistency throughout large pours necessary for monolithic circular foundations
Reduced segregation and bleeding, ensuring uniform quality throughout curved walls
5. Cost Efficiency
Optimized particle size distribution results in better cement utilization
Bangur PPC's pozzolanic content reduces cement consumption while maintaining performance
Lower maintenance costs over time due to enhanced durability properties
6. Environmental Considerations
Bangur Portland cement composition incorporates industrial byproducts, reducing overall carbon footprint
Manufacturing processes designed to minimize energy consumption
Contributes to green building certification points when used in sustainable construction
7. Consistent Quality Control
Stringent manufacturing standards ensure batch-to-batch consistency
Regular testing protocols maintain quality parameters above industry requirements
Reliable performance in new house construction projects across varying environmental conditions
8. Local Availability and Supply Chain
Well-established distribution network ensures timely delivery
Regional manufacturing reduces transportation carbon footprint
Consistent availability prevents construction delays
9. Proven Track Record
Successfully implemented in numerous circular and conventional building projects
Documented performance in structures across diverse climatic conditions
Trusted by professional builders and architects for challenging architectural designs
10. Technical Support
Comprehensive technical guidance available for specialized applications
Detailed documentation for achieving optimal mixes for curved structures
Professional support for addressing site-specific challenges
This is why a major section of architects, builders, and other construction professionals widely regard Bangur as one of the best cements for construction. If you would like a quotation for your cement order, contact us here.
Frequently Asked Questions
Q: How does Bangur Cement's quality compare to other leading brands in the Indian market, particularly for constructing homes in high-moisture regions?
A: The moisture resistance of Bangur Cement surpasses every other cement variety, particularly in wet environments. Because of its strong resistance against water and sulphate attacks this material provides dependable solutions for wet conditions during rain periods. Independent organizations confirmed that its revamped formula provides moisture resistance surpassing 15-20% of those of other standard cement mixes. The longevity of new house construction with Bangur Cement extends further as they need minimal maintenance in areas exposed to high rainfall zones.
Q: How many bags of OPC and PPC cement are required to build a single-story home in India?
A: When building a 1-story residential property spanning 1,000 to 1,200 square feet in India, you would require between 400 and 600 eighty-kilogram bags of cement. Multiple vital elements determine what quantity of cement you need to purchase. Your house-building requirements depend heavily on six fundamental elements: foundation type, soil quality, wall thickness, design complexity, floor type, and intensity of finishing work. You should estimate cement usage for house construction at 0.4 to 0.5 bags of cement per square foot.
Q: How does Bangur Cement's quality compare to other cement brands available in the Indian market, and what makes it suitable for specialized structures like circular buildings?
A: You can rely on Bangur Cement as a top choice for implementing curved formwork applications. This cement contains fine particles blended with an effective mix of chemicals, thus surpassing most other Indian cements. The cement's properties allow easy handling while maintaining excellent sticking properties. You can safely pour Bangur Cement into curved molds at its suitable setting time without facing any difficulties. The bending strength of this product cooperates with equal stress dispersion inside circular buildings. The test results from independent entities show that Bangur Cement shows excellent behavior during curved applications.
Q: What factors beyond cement grade should homeowners consider when selecting cement for their construction project, and how do these impact long-term durability?
A: Normal householders must consider numerous essential factors that go beyond cement types because they also need to think about regional soil characteristics and environmental influences. Cement selection based on environmental conditions and soil chemistry behavior constitutes a critical engineering practice that directly determines structure lifespan. Structural longevity and building integrity are maintained through reliable brands and building code standards as well as proper curing, which stands as the most significant factor in supporting these outcomes and lowering maintenance needs.