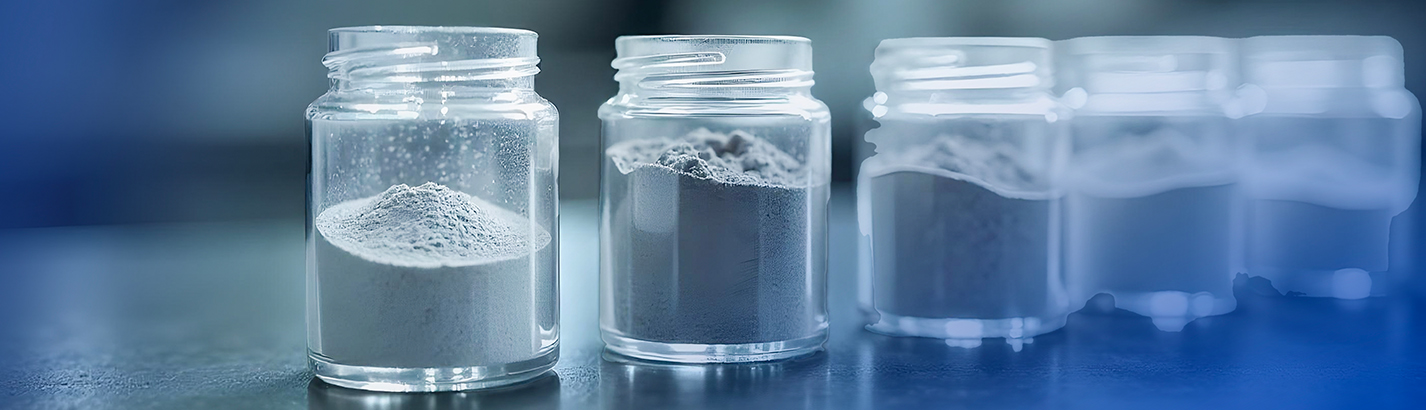
What are the Top 4 Types of Cement for Construction in 2025?
- Dec 20
- 6 min read
The Indian market offers builders and real estate developers several options when it comes to purchasing cement, but investing in the best cement for construction is not about getting your hands on the most reasonably priced bag of concrete. Buying cement for construction is about striking a balance between quality and affordability. As of April 2024, India’s net consumption for cement stands at 553 million tons per annum. By the end of the fiscal year, this figure is expected to climb the ballpark of 586-589 million tons per annum (MTPA) and touch the 600 MTPA mark by 2025.
For real estate construction, there are four preferred cement types that you can invest in-
1. Ordinary Portland Cement (OPC)
Ordinary Portland Cement is arguably the most-consumed top-rated cement for homes. As such, there is a vast amount of information on the material and how to control its workability, durability, or strength. At the nanoscale, the dominant phase of OPC is the Calcium Silicate Hydrate (CSH) gel, an X-ray, amorphous product with variable composition and structure. The CSH gel is the glue that aggregates with other crystalline hydration products, giving cohesion to the material, and therefore responsible for its mechanical properties and durability.
Ordinary Portland Cement consists of phases C3S (Alite), C2S (Belite), C3A (Aluminate), C4AF (Ferrite), free CaO, Alkali sulfates (R2SO4) and CaSO4·nH2O. The first four constitute about 85-90% of OPC while other constituents are present in smaller proportions totalling 10-15%. OPC can be graded into various strength classes defined by 28-day compressive strengths of cement mortars by manipulating the relative proportion of the four principal phases and concurrently adjusting their fineness of the product.
Although OPC is an immensely popular variety of concrete among the best cement brands in India and an essential ingredient for concrete-based constructions, it is responsible for rampant emission of carbon dioxide during the course of its production. To cut down on the increasing emission of CO2, researchers have been meticulously working on an alternative, sustainable binder that consists of slag, fly ash, palm oil fuel ash, metakaolin, rice husk ash, etc., alongside alkali-activators.
2. Portland Pozzolana Cement (PPC)
Portland Pozzoland Cement is made up of lime, silica, alumina, and iron oxide in an intimately grounded form. The mixture is heated at extreme temperatures in a kiln to form Portland clinker which is further ground with fly ash or calcined clay. The pozzolana constituent should be in the range of 10-25% by mass of PPC. Natural gypsum may be added during the grinding process.
The Bureau of Indian Standards (BIS) has standardized that the surface of PPC must be at least 300m2/kg. When water is added to PPC, it reacts with the lime and alkalies present in the PPC to provide strength to the concrete. BIS standardized PPC has an initial setting time of 30 minutes. At 3 days, BIS standardized PPC has a compressive strength of 16 MPa; at 7 days it should be 22 MPa, and at 28 days it must be at 33 MPa.
The hardening of PPC concrete due to the loss of capillary water causes dry shrinkage. PPC is considered to be more sustainable than OPC because it uses recycled materials such as fly ash in production. It is advantageous to use PPC because it has a low heat of hydration which helps cut down on cracks in the concrete. PPC is inexpensive, which makes it an economical construction material that is resistant to sulphate attacks and therefore perfect for hydraulic and marine structures.
3. Sulphate Resistant Cement
Sulphate Resistant Cement is the best option for projects that are erected on soil with a high concentration of sulphates. Sulphate Resisting Cement (SRC) is specially formulated as a hydraulic cement in building construction to withstand the corrosive effects of sulphates in water. SRC has specific additives and a low percentage of tricalcium aluminate (C3A) in its composition, which makes it highly resistant to sulphate attacks.
SRC is a special type of Portland cement where the C3A content is deliberately restricted to less than 5% and (2\C3A + \C4AF) is controlled to be below 25%. There is limited formation of calcium sulpho-aluminates which are formed from the reaction between calcium sulpho-aluminate and sulphate salts. This deliberate reduction in tricalcium aluminate minimizes the formation of sulphate salts thereby mitigating the corrosive impact on the concrete.
SRC is ideal for marine construction due to resistance against sulphate-rich seawater. SRC is top-rated cement for homes with foundations in areas with sulphate-rich soil, for example, in sewage treatment plants to resist chemical attacks. It is recommended for use in coastal regions for ensuring durability, which results in a higher cost in comparison to standard cement types. It offers maximum resistance to chloride ions reducing the risk of reinforced steel corrosion. SRC ensures enhanced workability and pumpability.
4. Blended Cement
Blended cement is also gaining popularity as the best cement in India for house construction across India. It comprises a mixture of portland cement and blast furnace slag (BFS) or a mixture of portland cement and pozzolan fly ash. Blended cements in concrete reduces mixing water and bleeding, improves finishability and workability, which enhances sulphate resistance, inhibits the alkali-aggregate reaction and lessens heat evolution during hydration, thereby modulating the chances for thermal cracking on cooling.
Blended cement with 70% slag cement is called Portland slag cement and used for general construction. It produces a low heat of hydration. The slag should be more than 50% and up to 70%. It is used for marine and offshore structures in soils with high chloride and sulphate content. Portland slag should be used for construction of water treatment plants and sewage disposal units where dissolved chlorides and sulphate ions pose a problem.
Portland-pozzolan cement used in general construction can contain up to 50% pozzolan. Fly ash is the most common pozzolan used in blended cement. It produces a low heat of hydration and reduces the leaching of calcium hydroxide. It is used in the construction of hydraulic structures like dams, retaining walls, marine structures like bridge footings under aggressive conditions, masonry mortar, and plastering.
Portland-limestone cement is relatively new to the market and contains 5-15% limestone. Ternary blended cement which comprises Portland cement and two other materials blended together to create a binder.
For further guidance on which cement works best for your project, contact us here.
Trending
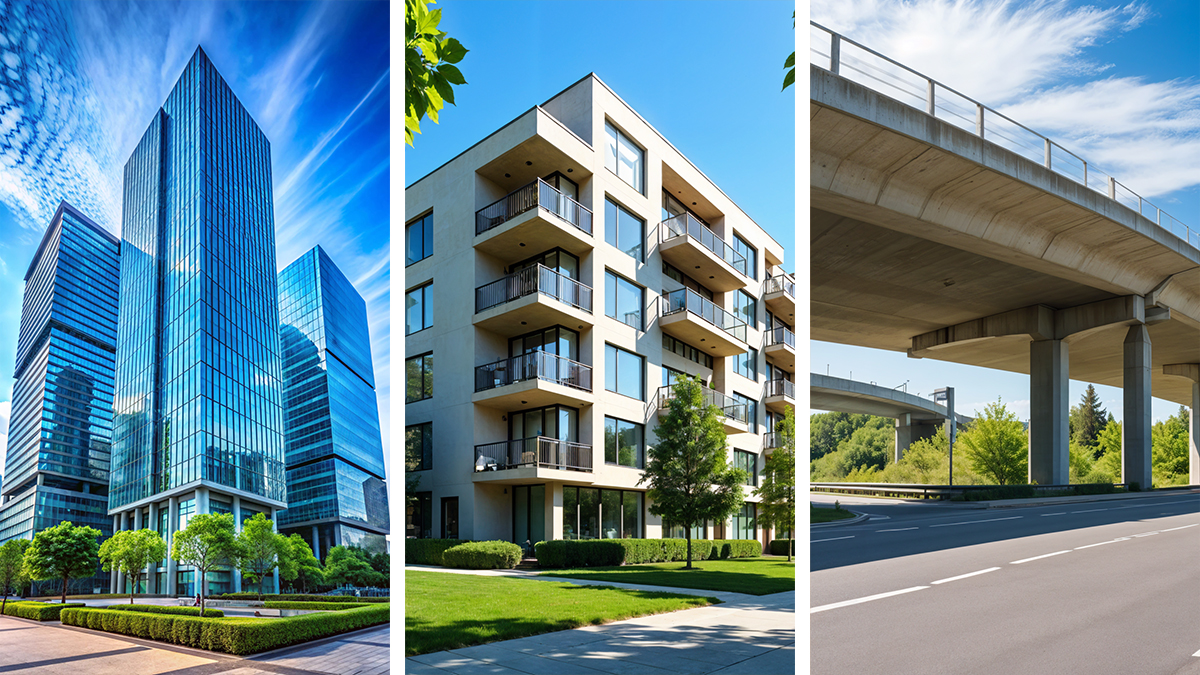
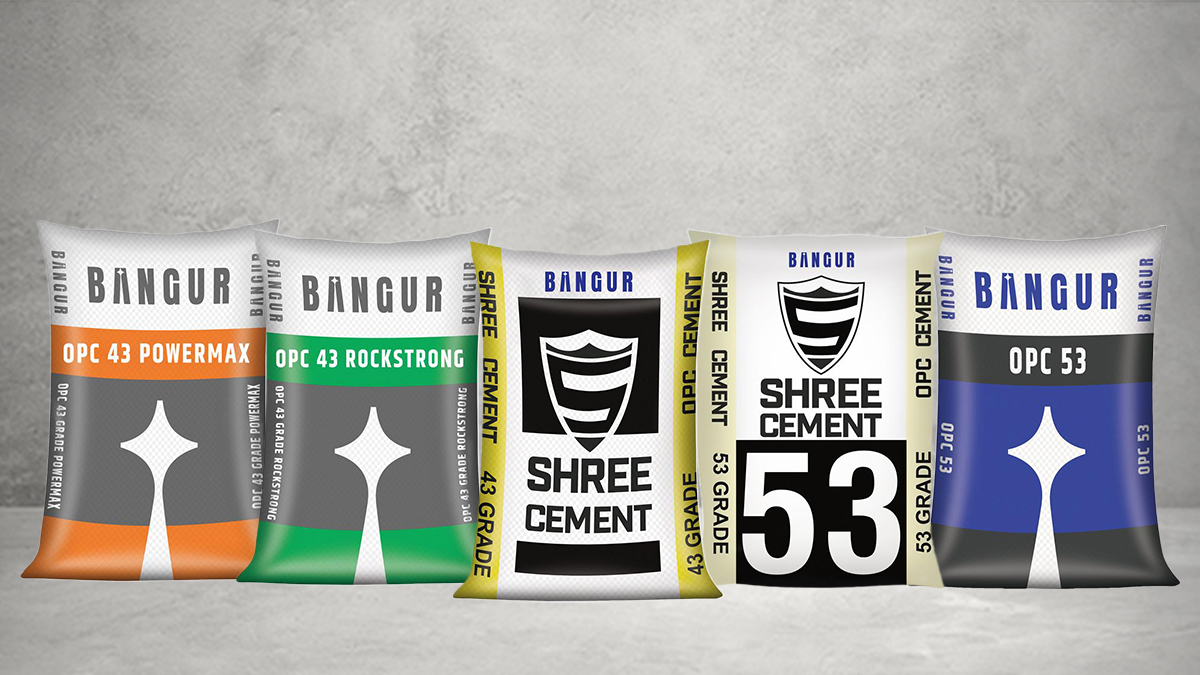
Understanding the Differences Between Cement Grades: 33, 43, and 53
- Nov 29
- 1 min read
Learn about the key differences between cement grades 33, 43, and 53. This guide explains their strengths, uses, and which grade is ideal for your construction project, helping you make the right choice for quality and durability.